What Are The Basic Steps Of Manufacturing Composites?
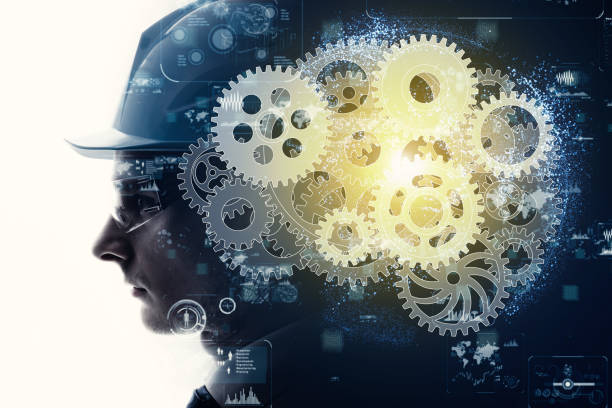
Composites Manufacturing is a process which makes use of various components
and techniques to produce a final product that is more durable and stronger than
traditional materials. This process can be used in many different industries
that range from construction to transportation. This article will provide an
overview of the essential steps of composite parts manufacturing and
explain the reason why it's such a valuable tool.
These are the four major steps in composites production. However, the order
of the operation may differ depending on the type of application or
manufacturing process.
Impregnation
The resin is then applied to the previously dried fiber. This makes sure that
the fiber is completely coated throughout the process. The outcome of this
process is known as the lamina. Different techniques are employed to obtain a
uniform and complete impregnation, although automation is the most commonly used
method today and uses the compaction roller to make sure that the resin flows
uniformly across fibers.
For example, in a filament winding process fibers are pushed through the
resin bath to impregnation. When a hand-lay-up procedure is used the materials
are already impregnated by the supplier of the material in a controlled setting
are utilized. This is done at the impregnation line in the automated fiber
placement process. Preparation is the name given to the end product of an
impregnation device.
Layup
The composite laminates are made by either using the fiber after impregnating
it or by placing the fiber/resin preregs at the desired locations and in the
desired orientations. The composite part thickness is built up by placing
different layers of the material.
The relative motions between the mandrel and the carriage unit affect the
distribution of fibers within filament winding. The fiber has directional
strength, and has to be placed in a specific orientation.
The preform, which is dry, is inserted inside a mold, allowing it to be
infused with the RTM process. The preform is made by braiding, AFP, cutting
& kitting etc. The resin is then injected into and then consolidated to form
the laminate.
Consolidation
When a consolidation process is carried out it is the application of pressure
to create the monolithic form from distinct plies while simultaneously
eliminating any voids or volatiles, while to achieve the desired volume fraction
of fibers within the component, and attaining the right dimensions and
tolerances.
The pressure is obtained by vacuum, compaction or pressing or wrapping. Most
epoxy resins carbon fiber parts manufacturing utilize vacuum as a method of
consolidating. The AFP methods apply the consolidation force at the time of
layup with a compaction roller. RTM will consolidate during the process of press
impregnation. When winding filaments the force of consolidation is initially
applied during winding, and then by wrapping the winding under tension with a
thin film of plastic.
Solidification
Solidification is the final step. It could be less than a minute for
thermoplastics and up to 120 hours for thermosets that use thermosets. For
proper consolidation, either vacuum or positive pressure is maintained.
The rate of solidification in thermoset composites is contingent on the
formulation of the resin and the cure time. To speed up the cure of the resin,
heat is used during the process of solidification. For thermoset resins usually
the higher the temperature at which the cure is completed more rapid the
cross-linking process. However, careful attention must be paid to the data sheet
of the material in order for the best result.
In thermoplastics, there's no chemical change during the process of
solidification. Therefore, solidification takes the most time and temperatures.
The cooling rate is what determines the rate at which thermoplastic processing
occurs. The process will yield more plastic if it has a shorter time for
solidification.
Summary
The world of composites has many conditionals, therefore making a blanket
statement can be difficult, however the four steps listed below are most common
elements in all composites production processes regardless of whether the
product is thermoplastics or thermosets. The order and methods of carrying out
the steps may differ based on the type of material, the manufacturing process
and the final requirements.
The thermoplastic and prepreg materials are used to impregnate the fibers before the layup. They are most commonly employed in aerospace manufacturing where the standards are high. Parts with lower requirements that are used for leisure and sports equipment (excluding high-performance equipment), would generally perform the layup and then inject the fibers using resin. Consolidation is independent of it being solidified, but parts cannot be treated (thermosets) or solidified (thermoplastics) without simultaneous consolidation.
Comments
Post a Comment